Pikes Peak
Summit Visitor Center
The Pikes Peak Summit Visitor Center was the highest ongoing construction site in North America during its construction. This challenging project created a facility that takes advantage of the inspiring views and natural beauty of Pikes Peak, also known as America’s Mountain.
Colorado Springs, CO
Pikes Peak - America's Mountain
RTA Architects & GWWO Architects
38,000
Mountain Majesty
The Big Picture
Each year more than half a million people visit the summit of Pikes Peak, which sits 14,115 feet above sea level. The new visitor center replaces the existing Pikes Peak Summit House and features an immersive visitor experience. The new facility was designed so that visitors can focus on the beauty, richness, and scenery of America’s Mountain, with multi-media exhibits to tell the story and history of the mountain and enhance the experience.
Started in June of 2018, the complex took three years to complete. With a short work season atop the mountain (late spring to late fall, weather permitting), each day’s shift was shortened to keep workers safe from the effects that can be suffered at altitude.
GE Johnson started the project by relocating the central utility plant, blasting, and moving dirt and massive boulders for the foundation of the new Visitors Center. These materials were stored on site for reuse, with limited laydown areas.
Ingenuity in Action
A jobsite on top of a Colorado 14er presents special challenges for the workers. To create a safe work environment and contribute to the overall success of the project, GE Johnson required all crew members to undergo an extensive physical examination, including a flexibility test and a Harvard Step fitness assessment. Crew members then engaged in a two-hour, site-specific orientation, followed by a briefing on the special safety measures necessary for working at high altitude.
The structure is built on bedrock that is beneath the permafrost layer of the mountain to reduce the likelihood of shifting and movement of the structure. To improve building efficiency, foundation forms with reinforcing steel were prefabricated offsite and delivered to the summit, minimizing the amount of work being performed on the site.
The visitor center was constructed to meet The Living Building Challenge – the world’s most rigorous proven performance standard for buildings. Considerations in meeting this goal included restoring the building’s interrelationship with nature; creating environments that optimize physical and psychological health and wellbeing; and using materials that are safe for all species through time. Meeting this challenge required a strong partnership among the City of Colorado Springs, the design team, GE Johnson, and all of the subcontractors. Though the Living Building Challenge compounds the already immense challenges inherent in this project and its location, it is a testimony to the commitment made to the responsible stewardship of natural resources.
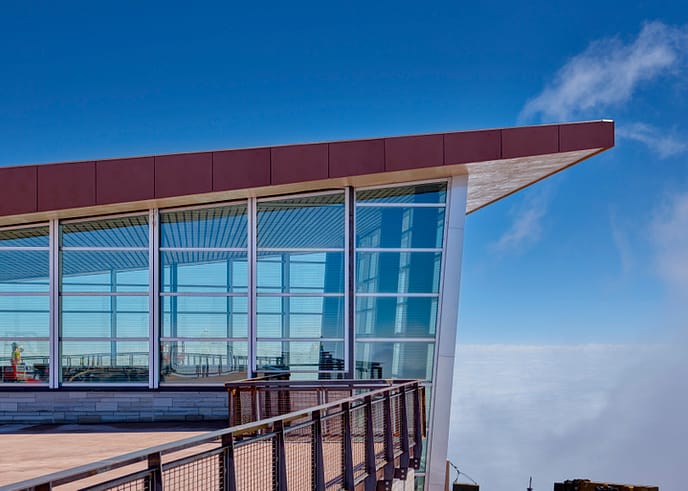
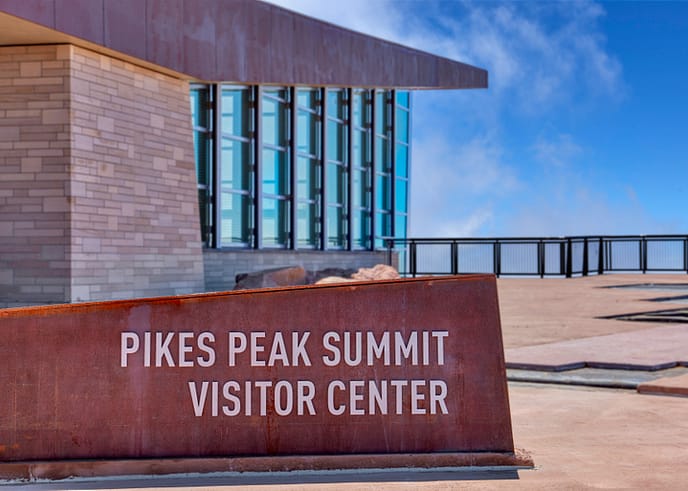







The little details
- The southern orientation of the new building takes advantage of the enhanced solar gain at altitude, harvesting daylight and using photovoltaics to generate electricity.
- GE Johnson purchased a special truck that can navigate the switchbacks on Pikes Peak Highway to haul equipment and materials to the summit.
- The project is pursuing LEED Platinum Certification and will be built to meet The Living Building Challenge requirements. (additional details provided below)
FIRST Living Building Challenge project to be constructed in Colorado (in progress) - Pursuing LEED Platinum Certification
- Bioclimatic design for Net Zero Energy
- Thermal mass to reduce mechanical heat rejection by 40%
- Dynamic glazing to reduce cooling needs
- Varied thermal setpoint strategy, to accommodate different space needs and maximize heating/cooling efficiency
- Circulating water throughout building to level out cooling energy will save 10%. Circulating hot water through building in radiant system will save 35% heating energy use.
- Heat recovery through space heating and exhaust air will be transferred to radiant loop and save 8% energy use.
- Overall energy reduction of 42% energy cost savings prior to renewable energy strategy
- Net Zero Waste
- Goal of project is to divert 90-99% of material waste from the landfill. Current infrastructure in Colorado makes this challenging. We have partnered with Recycle Colorado (formerly CO Association for Recycling) to further the Colorado Contractors Challenge which should help drive demand for increased infrastructure. We are also finding other ways to partner on the development of infrastructure that can support a broader range of material reuse.
- Net Zero Water
- 90% of water load comes from toilets
- Freshwater usage reduced by 66% (prior to graywater use)
- Water is hauled up and wastewater is hauled down the mountain. Reduced freshwater trips from 127 to 72, and wastewater trips from 174 to 69, which saves gas & transportation impacts on top of water use reduction
- Vacuum toilets save 80% consumption
- Faucets save 5% consumption
- Waterless urinals and low water-use kitchen equipment save an additional 5% consumption
- Project had to use vacuum toilets in lieu of composting toilets to create an end-use for graywater. Graywater use, once implemented, will increase water use reduction by 77%overall.
- Building is designed to be Net Zero water-ready, including rainwater/snow harvest and reuse in the future
- Built into the mountain, extensive dynamic glazing on one side to retain views, mitigate heat gain and loss, and decrease first and maintenance costs associated with shades